Dragline mining & demolition explained

Draglines are heavy-duty excavating tools used to remove overburden in open-cut mines across Australia. While this huge piece of machinery can be highly productive and cost-effective, it will not remain feasible forever. Eventually, an abandoned or decades-old dragline will need to be demolished and removed from the mine site.
Below, we explain how mine draglines work, including information on their methods, components, and demolition. Read on to discover more about dragline mining.
What is a dragline in mining?
A dragline is a mechanical excavator and crawler used during large-scale works. One of the biggest machines ever built, a dragline tends to weigh approximately 8,000 to 13,000 tonnes.
Smaller models are essentially composed of a winch drum on a lifting crane. Built offsite, they are generally used for civil engineering works, such as foundation, road and port construction, and can be easily dismantled.
Larger draglines are reserved for oil sands or coal surface mining. Assembled onsite, they stay in place for decades until demolition is required.
In mining, draglines get rid of overburden or, in other words, any material that is standing in the way of the target resource. For instance, removing the surface soil and rock above a coal seam. This overburden can then be stored and used to refill the open pit once mining operations cease.
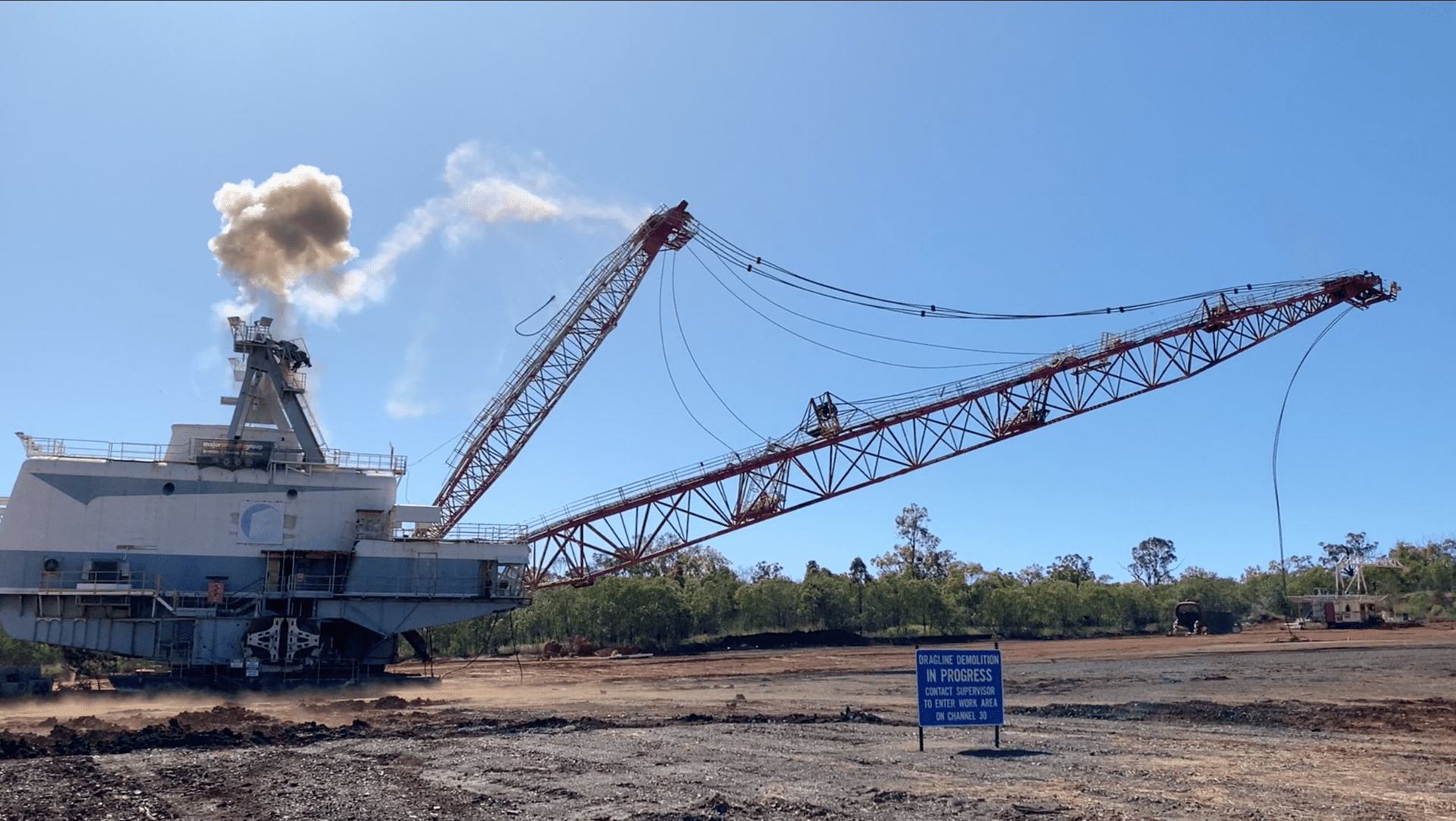
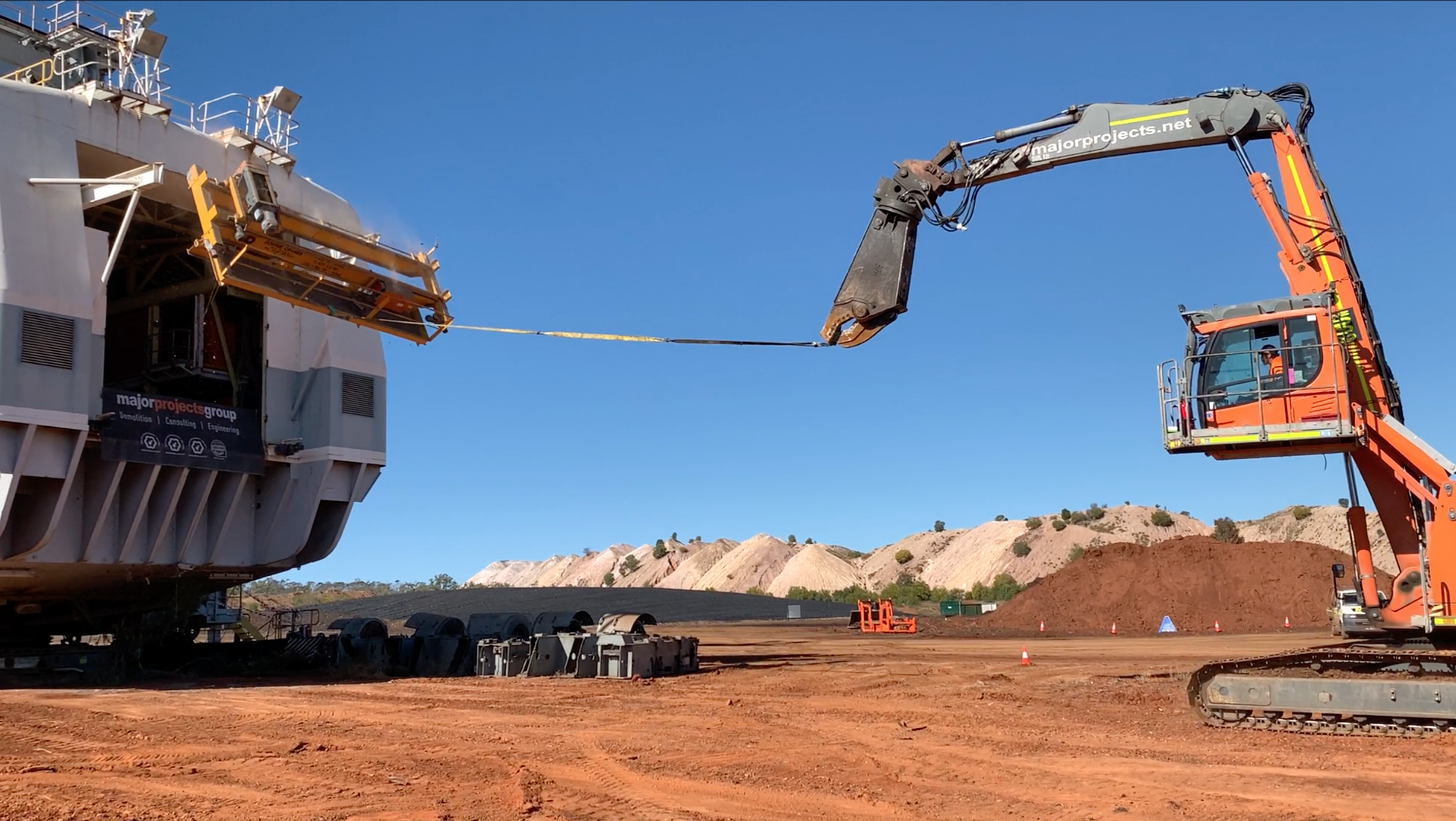
How do mining draglines work?
A mining dragline dismantles and moves overburden in a similar way to a crane. A massive bucket is cast out from the machine’s body and then pulled inwards, shovelling material along the way.
Multiple ropes are used to adjust this process, which enables your team to scoop up and dump material nearby in far less time than with a standard excavator.
Importantly, precise dragline mining methods depend on the size and model, which can offer various levels of drag, rotation and displacement.
Unlike the majority of machinery in mines, most draglines do not run on diesel. Instead, they are powered directly via the high-voltage grid, at voltages varying from 6.6 to 22kV. A typical dragline consumes up to 6 MW during standard mining operations.
5 key dragline components
1. Machine body
The machine body is the core structure upon which other components are assembled. It houses the dragline’s engines and operator’s cabin. Depending on its design, this body can feature continuous tracks or be placed on pontoons.
2. Boom
The boom is a metal structure that extends from the machine body. The hoist rope that holds the bucket hangs from this truss-like structure.
3. Bucket
The bucket is a toothed shovel or scoop that excavates, loads, transports and unloads overburden at the intended location. Depending on the dragline’s size, the mine site conditions, and the overburden’s properties, different techniques can be used to operate the bucket. However, this component can generally move up and down via the lifting cable or forward and backward via the drag wire.
4. Hoist rope
Also known as the lifting cable, this motor-driven rope hangs from the top of the boom. It holds the bucket away from the boom and is used to raise or lower it – all while supporting the hoist-coupler assembly.
5. Drag rope
The drag rope connects the machine body to the bucket. It can extend or retract to bring the bucket forward or backward, respectively, as well as adjust its inclination as required, in line with the lifting cable’s movements.
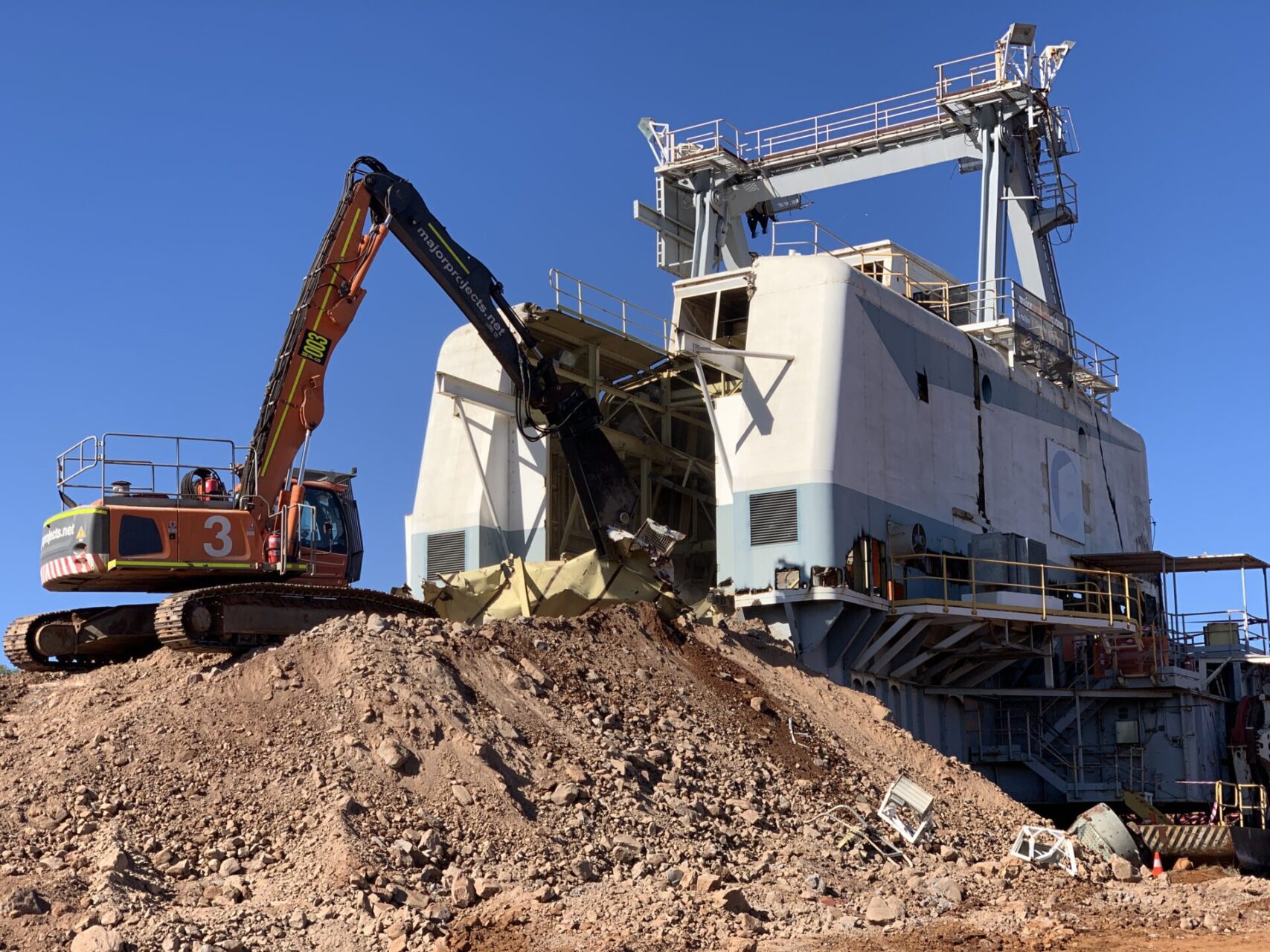
Mine dragline maintenance and shutdowns
When it’s time to service a dragline, you will need to implement a scheduled mining shutdown. Dragline maintenance can take anywhere from 4 to 12 weeks depending on its scope, and may be required several times a year.
This procedure involves work inside the confined space of the machine, with support and other tasks provided by spotters outside. Therefore, effective communication and strict Work Health and Safety protocols are both essential to your team’s safety.
Additionally, in some cases, it may be more cost-effective to dismantle or demolish an outdated mining dragline and replace it with a newer model.
The way forward for mining draglines in Australia
Compared to other mining machinery, draglines have remained relatively similar in design and operation systems. But that’s about to change. With manual operators causing up to 15% variation in product results, mining companies like CSIRO, MineWare and CRCMining are collaborating with the University of Queensland to develop automated systems that enhance efficiency.
This revolutionary technology identifies the most optimal sequence of movements for a mining dragline to excavate overburden. The aim is to provide operators with real-time guidance on position, digging and dumping, helping them to make informed decisions on dragline sequencing.
The result? A significant boost in productivity.
Mine dragline demolition
A mining dragline can be demolished with mechanical, explosive or induced collapse techniques, the most appropriate of which depends on site conditions and project requirements. If you are ready to remove and replace your old mining dragline, Major Projects Group is here to help. Our experienced dragline demolition contractors can take care of everything from decommissioning and dismantling to asset recovery and site remediation.
For example, Idemitsu recently engaged Major Projects Group as the Principal Contractor to demolish a Bucyrus Erie 1,260W dragline at the Ensham Resources mine site in Comet, Queensland. We performed 12 induced collapse demolition drops in total, recording over 3,300 man-hours and processing at least 1,300 tonnes of scrap steel – all of that with 0 safety incidents.
Explore more of our mining demolition projects.
Enquire about mine dragline demolition with Major Projects Group
Demolishing a mine dragline involves a plethora of processes, regulations and technicalities, so it is essential to engage an experienced contractor with a proven track record. Dedicated to excellence in dragline demolition, Major Projects Group has been trusted by many of Australia’s largest mining companies, including Glencore, Mach Energy Australia, Idemitsu, Rio Tinto and BHP Billiton.
As a Social Enterprise advocating environmental stewardship, we utilise the latest equipment and certified HSEQ management systems to complete even the most complex mine site demolitions.
Discover a full range of capabilities, including decommissioning, dismantling, asset recovery and asbestos and hazardous material removal – all of which are actioned via safe, compliant and cost-effective solutions.
To start your dragline demolition with Major Projects Group, please enquire today at +61(0)2-4967-7900 or [email protected].